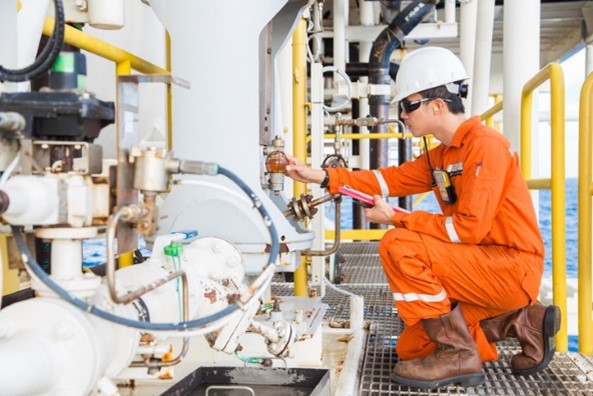
In-Service Piping, Pressure Vessels, and Storage Tank Inspection
Inspection Code: In-service Inspection, Rating, Repair, and Alteration of Piping, Vessels, and Tank Systems
Introduction:
Regular in-service inspections of piping, tanks, and pressure vessels are required to ensure their safety, dependability, and compliance with industry standards. This comprehensive step-by-step guide will assist you in comprehending the complexities of performing in-service inspections in accordance with the API 570, API 510, and API 653 Inspection Code. You will gain the knowledge and skills required to perform thorough inspections, ensure quality assurance, and maintain compliance by following these detailed instructions.
Step 1: Inspection Preparation and Planning
Determine Inspection Frequency:
To determine the appropriate inspection frequency, consider factors such as service conditions, corrosion rates, process requirements, and previous inspection history.
Consider the importance and potential risks associated with the piping, tanks, and pressure vessels.
Examine Previous Inspection Reports:
Examine previous inspection reports for trends, degradation mechanisms, and areas that require special attention.
This data can be used to plan the current inspection, prioritize areas of concern, and determine the scope of work.
Step 2: Visual Examination
External Examination:
Perform a thorough visual inspection of the piping, pressure vessels, and tanks, paying special attention to external factors such as leaks, corrosion, erosion, mechanical damage, and support integrity.
Pay special attention to vulnerable areas such as pipe connections, welds, and sections exposed to external forces or environmental conditions.
Internal Examination (If Accessible):
Inspect the internal surfaces of the piping, pressure vessels, and tanks whenever possible, using appropriate inspection tools or by entering through openings, manholes, or cleanouts.
Examine the system for signs of internal corrosion, deposits, pitting, scaling, and erosion that could compromise its integrity.
Step 3: Non-Destructive Testing (NDT)
Ultrasonic Thickness Testing (UT):
Use ultrasonic thickness gauges to determine the remaining wall thickness of the pipes.
Compare the measured values to the minimum required thickness specified by the relevant codes and standards.
Additional NDT Techniques:
As needed, use other NDT methods such as magnetic particle inspection, liquid penetrant testing, radiography, or advanced techniques (e.g., guided wave testing). These techniques aid in the detection of defects such as cracks, weld discontinuities, material degradation, and internal anomalies.
Step 4: Fitness-for-Service Assessment
Evaluate Identified Anomalies:
Compare any detected defects or anomalies to the API 570 standard's guidelines.
Determine their impact on the integrity, remaining life, and fitness for continued service of the system.
Classification and Recommendations:
Sort anomalies according to their severity, size, location, orientation, and expected remaining life.
Consult the API 570 guidelines to determine the correct classification and recommended actions (e.g., repair, further assessment, monitoring).
Step 5: Repairs, Alterations, and Compliance
Create a Repair Plan:
Create a comprehensive repair plan based on the inspection findings and anomaly classification.
Follow the API 570 specifications for repair methods, materials, and personnel qualification.
Standards Compliance:
Ensure that all repairs, alterations, and welding activities adhere to the relevant codes, standards, and regulatory requirements. Maintain accurate documentation of repair activities and adhere to established record-keeping procedures.
Step 6: Quality Control and Compliance
Implement Quality Assurance Measures:
Implement a strong quality assurance program that covers all aspects of the inspection process.
Regularly monitor and audit inspection activities to ensure compliance with API 570 and organizational standards.
Documentation and Reporting:
Keep detailed records of inspection findings, repair activities, compliance measures, and supporting documentation.
Create detailed inspection reports that include photographs, measurement data, recommended actions, and evidence of compliance.
Conclusion:
This detailed step-by-step guide provides a detailed framework for performing in-service piping, pressure vessels, and tanks inspections in accordance with the API 570 Piping, API 510, API 653 Inspection Code. Following these guidelines will provide you with the knowledge and tools you need to conduct thorough inspections, ensure quality assurance, and maintain compliance, protecting the integrity and reliability of your equipment.
API 570 PIPING INSPECTOR: CERTIFICATION PREPARATION COURSE
API 653 STORAGE TANK INSPECTOR: CERTIFICATION PREPARATION COURSE
API 510 PRESSURE VESSEL INSPECTOR: CERTIFICATION PREPARATION COURSE