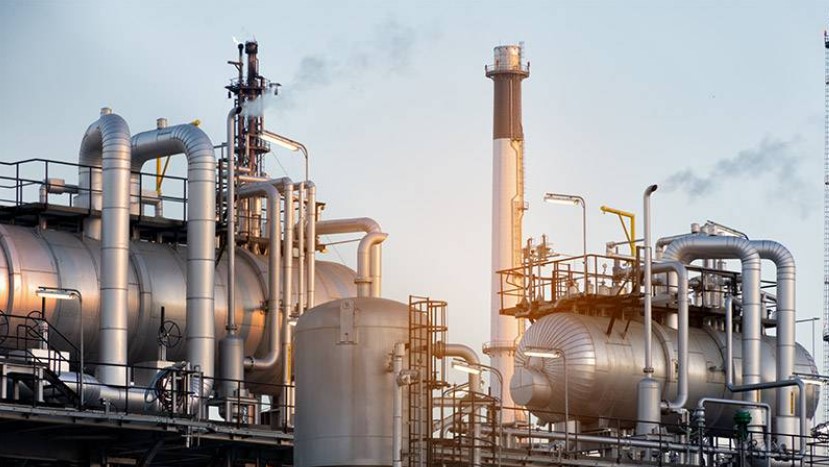
Construction of static equipment like vessels, tanks, and piping involves a meticulous process ensuring safety, functionality, and adherence to design specifications. Here's a breakdown of the typical stages:
1. Pre-construction Phase:
Engineering and Design:
Detailed engineering creates blueprints, material specifications, and construction procedures.
Pressure vessel design follows codes like ASME Boiler and Pressure Vessel Code (BPVC) or relevant international standards.
Piping design adheres to codes like ASME B31 Piping Codes, considering pressure, temperature, and fluid compatibility.
The construction of steel structures involves adherence to a comprehensive set of codes and standards that cover all aspects from design and materials to fabrication and erection. Like AWS, AISC, ASTM..etc.
Material Procurement:
Required plates, pipes, flanges, and other components are procured based on specifications.
Material certifications ensure adherence to quality standards.
Fabrication Shop Preparation:
The fabrication shop prepares the workspace, tools, and equipment for construction.
Welders and other craftsmen undergo qualification tests as per code requirements.
2. Construction Phase:
Vessel and Tank Construction:
Plate cutting to precise dimensions using CNC machines or manual methods.
Plate shaping and forming using rolling machines or presses.
Welding of plates to create vessel shells and tank walls, following qualified procedures and inspection protocols.
Nozzle attachment for connections to pipes and instruments.
Heat treatment of welds for stress relief, if required by the material and code.
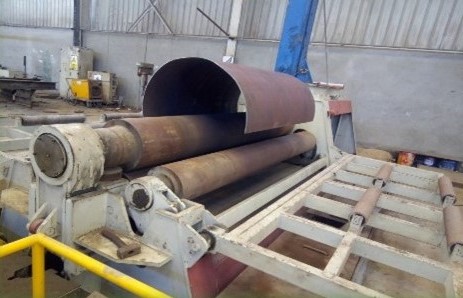
Piping Fabrication:
Pipes are cut to specific lengths based on the design layout.
Pipe ends are prepared for beveling, threading, or flanging based on joint type.
Pipe sections are joined using welding, threading, or flanging techniques as per design and code requirements.
Supports are installed to ensure proper pipe placement and prevent excessive stress.
Non-Destructive Testing (NDT):
Welds and critical areas undergo NDT like radiography, ultrasonic testing, and magnetic particle testing to detect any cracks, voids, or imperfections.
Ensures weld quality and vessel/piping integrity.
3. Post-construction Phase:
Inspection and Testing:
Final inspection by qualified inspectors verifies adherence to design and code specifications.
Pressure testing (hydrostatic or pneumatic) ensures the vessel/piping can withstand designed pressure.
Leak testing confirms a perfect seal throughout the system.
Painting and Insulation:
Vessels and pipes are painted for corrosion protection and aesthetics (if applicable).
Insulation may be added for temperature control or personnel protection.
Documentation:
As-built drawings and documentation are compiled, reflecting any deviations from the original design.
Material certifications, weld test records, and NDT reports are included for traceability.
Additional Considerations:
Safety: Safety protocols are paramount throughout construction, with proper personal protective equipment (PPE) and adherence to safe work practices.
Quality Control: Stringent quality control procedures ensure all steps meet code requirements and design specifications.
Schedule and Budget: Construction adheres to a pre-defined schedule and budget to ensure timely completion within cost constraints.
By following these steps and maintaining high standards, static equipment like vessels, tanks, and piping can be constructed safely, reliably, and according to design intent for various industrial applications